Articulated Mixer Design
- Lee White
- Nov 7, 2024
- 3 min read
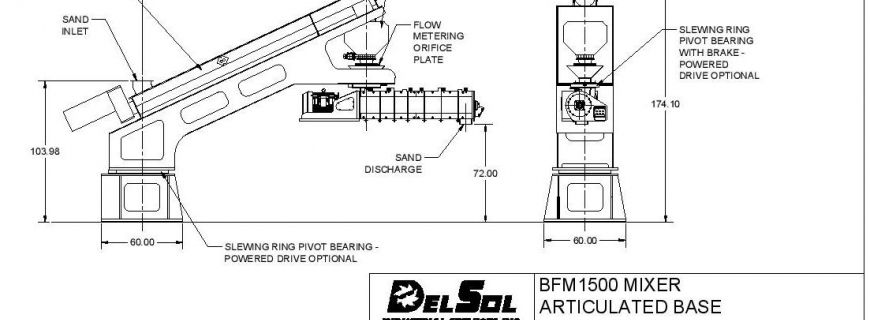
Del Sol is pleased to release the design of our Articulated Mixer Base. It is available for the BFM750, BFM1500, and BFM2500 mixers. We started with a clean sheet mentality and wanted to design around today’s needs of the foundry industry. To that end, we have made several improvements over other units available on the market:
5 or more years ago, few were concerned about airborne silica. “Yeah, it’s dusty – who cares?”…. As we all know, that stance has changed and equipment needs to be designed to reduce the amount of airborne silica as much as possible. Most articulated mixers on the market use a series of open belts and funnels to deliver sand to the mixing chamber. At each transition point, there is a cloud of dust/silica when the machine is running. In order to avoid this issue with our design, we have replaced the feed belt with an enclosed auger and a sealed surge hopper built into the arm. This design completely encloses the sand stream from the sand inlet to the mixer discharge, allowing no exit points for dust/silica to get airborne prior to the mixer discharge. Also, with being fully enclosed, there are no points where the sand will leak out into a big pile on the floor by the mixer base.
With this auger design, we are able to carry the sand at a steeper angle than a smooth or rough-top belt, which allows us to achieve a lower mixer inlet height than others.
By adding the surge hopper in the arm directly above the mixing chamber, we are able to utilize our Butterfly Valve/Fixed Orifice Plate Sand Gate System for sand calibration. This is a simpler system than adjusting belt speeds or changing dam heights in order to modify calibration. This also makes it so that the sand is metered immediately in front of the mixing chamber rather than back at the back of the belt. This is what Del Sol calls “Metering Where It Matters”.
As sand reclamation and re-use has become more prevalent, we have seen that mixers more often need to be capable of mixing multiple sands and often at different rates. For example, an operator may want to run new sand at a low rate while facing and tucking, and then run reclaimed or blended sand in at a high rate for bulk fill to save time. The belt style mixers were developed in a time where there was typically one sand and a single rate, but then capability was added to them as the needs arose. The issue with this is that the sand selection and rate are controlled back at the inlet to the belt, meaning that if the operator makes a selection change, the mixer will continue to run at the previous selection until the sand that was already on the belt has been purged. Also with the belt style when equipped with multiple sands/rates, there could still be another 200-300 pounds of sand that has to be purged from the belt at the end of each cycle, meaning once the operator switches the machine off after a pattern is filled there is still a lot of sand coming. To address this issue with our design, we use our Surge Hopper/Butterfly Valve System directly above the mixing chamber, meaning that any sand selections or rate changes will be instantaneous, with no need for belt purging. Once again, “Metering Where It Matters”. For multiple sand installations, we install two augers so that the sand setting change is immediate and metering is proper.
Both pivots are fitted with slewing rings that are a standard catalog size available from a well-known slewing ring manufacturer with USA-Based Offices. Gone are the days of trying to find a one-off slewing ring replacement for an old machine.
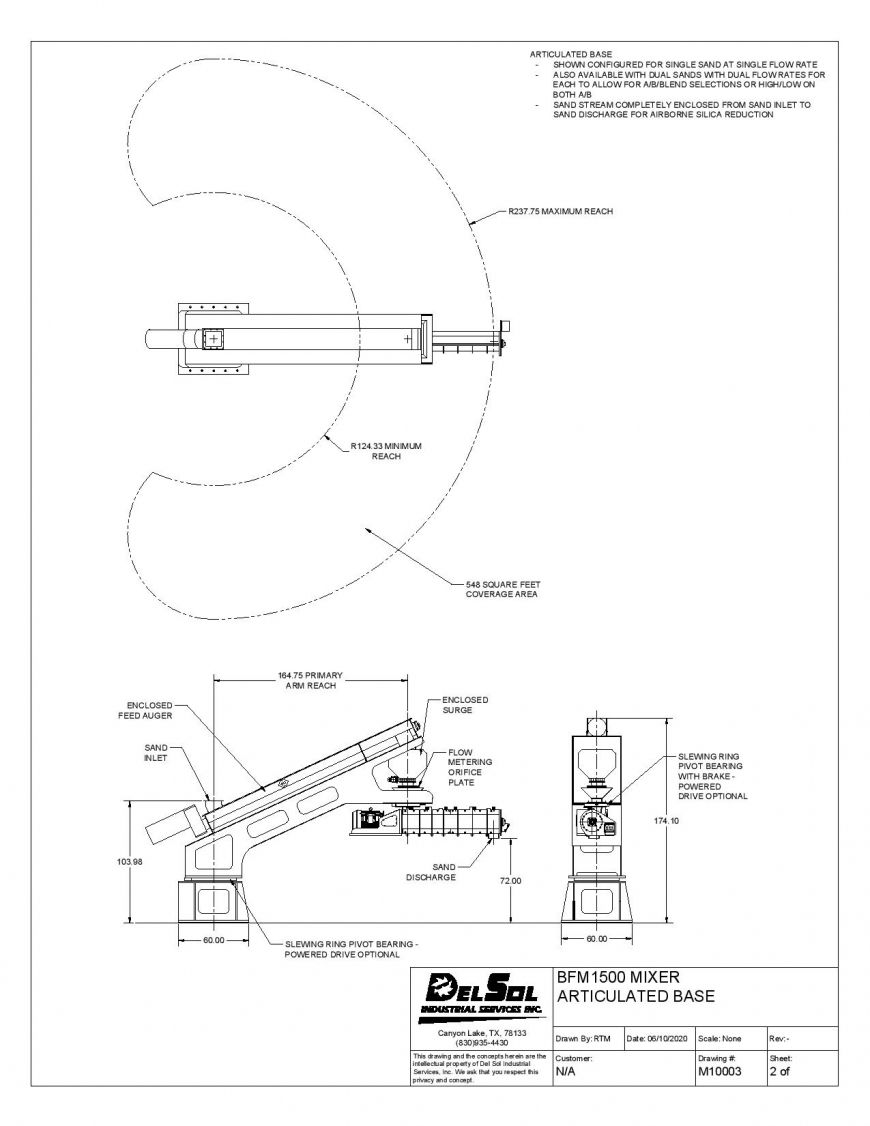
Posted by Del Sol Industrial Services, Inc.
